- In-wheel motor maker Elaphe doesn't see issues with durability or unsprung mass
- "Vehicle-level" integration of tech could bring 20% cheaper vehicles, 20% efficiency boost
- Elaphe is targeting 95% efficiency on a battery-to-wheel basis by 2030
If you took a quick look at the display stand for Slovenia’s Elaphe Propulsion Technologies at CES 2025 last month, you might have walked away with the message that the supplier of in-wheel motors has moved on from Aptera, Lightyear, and Lordstown and is pitching its tech to cars that are fast, exotic, and expensive.
That much is true—in the short term. Long-term, Elaphe has a grander global vision than just fitting into the performance picture.
In the meantime, it sees performance vehicles as the perfect venue for showing tech-savvy car buyers what in-wheel motors can do. At CES, Elaphe revealed a revised in-wheel motor design, called Sonic 1, that’s compatible with larger, track-ready brakes and high-performance vehicles.
In a rear-engine, rear-wheel-drive model, for instance, it could deliver “something extra,” as brand and marketing architect Iztok Franko put it, at the front wheels without redoing the architecture of the vehicle—as part of a hybrid performance upgrade.

Elaphe Sonic 1 in-wheel motor for performance cars. - CES 2025
The Sonic 1 motors themselves, which it teases are likely to arrive in a production vehicle in 2026, can make up to 268 hp and 737 lb-ft each in their default form—designed to fit a 21-inch front wheel, as shown. And to take it to a scorching extreme, they’re being developed to fit up to 24-inch wheels, as Elaphe and its stand partner Italdesign teased in an updated Quintessenza supertruck concept, offering a hypothetical combined max of 1,600 kw (nearly 2,150 hp).
“So now we remove the obstacle of reengineering the whole vehicle, it’s easy to integrate, and you can upgrade the performance and upgrade the control of the car,” said Franko.

Italdesign Quintessenza concept
In-wheel tech promises simplicity, efficiency
If you compare it to an e-axle with an inboard motor, there are no additional mechanical losses, because it’s only one rotating part per motor. There are no additional bearings, gears, or added constant velocity joints, either.
It’s a good start to thinking about what in-wheel tech can do, and why it’s been popular for some vehicle types, like very large trucks and buses. But it’s only scratching the surface for what Elaphe and the few other companies see as a bright future applying the tech to passenger vehicles.
Green Car Reports caught up with Elaphe chief technology officer Gorazd Gotovac at CES about how its technology is evolving and found a company that sees in-wheel tech as a key part in the long-term future of the car.
Gotovac emphasized to Green Car Reports that over many years and iterations, the company has worked to fine-tune the design through inverter control and management of second-order effects in the physics of the magnetic field. Partly through that it’s achieved a 10% efficiency boost versus the previous generation of its motors, from fourth to its current fifth generation.

Elaphe in-wheel motor for Lightyear 0
By the time Elaphe gets to production in high volume, which it sees as around 2030, it’s targeting a 95% efficiency, on a battery-to-wheel basis, based on highway driving.
Its design uses permanent magnets, but Gotovac says that the company has already confirmed that by 2030 it will be able to bypass the use of heavy rare-earth materials, keeping to lighter rare-earths instead and reducing the environmental footprint.
“We believe that once in-wheel motors are adopted there will also be versions without permanent magnets on the low end of the market,” he added. “But it will bring some weight penalty.”
Unsprung mass isn’t such a big deal
In-wheel motors increase the amount of unsprung mass (all the mass not supported by the suspension), which auto engineers and insiders routinely claim makes ride and handling much harder to tune and complicates safety.
It’s simply not as significant of an issue as some vehicle engineers paint it to be, according to CTO Gotovac. That’s because wheels and tires, in combination, are quite heavy; add an in-wheel motor and you’re not at all doubling or tripling the weight, he explained to Green Car Reports. You’re boosting it by about 30% when figuring in the brakes and all the ancillary pieces. Factor in items that are redundant for in-wheel motors and the gain in unsprung mass can be as little as 35 pounds per wheel versus an inboard motor setup.
And adding in-wheel motors at the front wheels is an easier way to add hybrid propulsion while maintaining safety, argued Gotovac. “If you have a car which has been engineered and crash-tested and you want to hybridize it, you have to redo all the crash-testing,” he said. “But if you put in-wheel motors in, you don’t have to redo all the crash-testing, because actually the structure in front, it will be the same…and if you’ve done the engineering right the wheels are just going to hold onto the rest of the structure.”
Elaphe’s units are designed to survive minor collisions, and it means that the body doesn’t need a crash structure designed around incompressible powertrain pieces.

Lordstown Endurance
Durability work already done on in-wheel motors?
What makes in-wheel motors fundamentally different than existing inboard motors is that the motor’s rotor spins directly with the wheel and its stator acts as the hub. Because of this, they’re subject to higher levels of vibration and road shocks, but Elaphe’s Gotovac insists that durability is no longer a concern. In recent years it has pushed its full validation cycle for the vehicle lifetime of its motors out to 300,000 miles, from the previous 150,000 miles.
Lordstown Motors would have provided that real-world evidence of durability for Elaphe, in its Ohio-built Lordstown Endurance electric pickup, using U.S.-built motors from the Slovenian company—if it weren’t for Lordstown’s demise in June 2023.
As Gotovac emphasized, the design of the motor that Elaphe still follows was fully validated in the Endurance, but it was a different application as Elaphe itself didn’t have anything to do with the inverters, which allow a finer level of motor control. In a drive of the Lordstown Endurance, Green Car Reports didn’t have any issue with motor response, ride, or handling of the electric truck.

2023 Lordstown Endurance
One of Ford’s top EV executives, Darren Palmer, told Green Car Reports in 2021 that it nixed in-wheel motors as a possibility in the F-150 Lightning electric truck over concerns about durability. And Aptera dropped in-wheel motors for its production-bound three-wheeler in what appeared to be an issue not with any of those concerns but with cost.
At present, there are some, but relatively few, examples of mainstream models that offer these motor types. China’s Dongfeng, in 2023, claimed to be building the world’s first passenger car with in-wheel motors—powering the rear wheels in that case, supplied by Protean Electric.
In the meantime, in-wheel motors continue to look like the future, albeit a future without any significant present-day commitment—and plenty of false starts. Perhaps backing up Elaphe’s claims that they’re the best solution for the future, Hyundai and Toyota have continued to develop their own in-wheel motors, or at least remain involved in their development.

Lightyear with Elaphe motors
In-wheel motors remain mass-market-bound
As Elaphe’s Gotovac explained to Green Car Reports at CES, the company sees niche high-performance applications like Sonic 1 as an important step in getting the word out about in-wheel motor technology and how it can perform to extremes. But it has bigger-picture ambitions at the affordable end of the market.
This is the fifth generation of Elaphe’s motors and it’s been simultaneously working toward higher power density and better performance while also keeping an eye on how the tech can truly be applied to the mass market.
Gotovac said that while selling automakers on the idea of in-wheel motors for mass-market EVs has proven challenging, the technology can potentially pay much greater dividends.
“We are able to develop this power-dense design that we have into something that is cost-effective for a car that doesn’t have to be as powerful,” he explained. “If you’re using less material to get more power out of it, and if you’re not using exotic materials, then your potential for cost is better than the previous generation.”

Aptera with Elaphe motors
In-wheel motor potential: Ride, handling, identity
Elaphe’s Sonic 1 motor system is designed to use an inverter from its official partner McLaren Applied Technologies, with software developed with that firm—and the key to some of those special control strategies is the software.
But Elaphe emphasizes that the potential for in-wheel motor tech rests on much more than power delivery. Once you have it at each wheel, all sorts of opportunities arise for the motors to take an active role in: ride, handling, stability control, and even communication to the driver.



Aptera with Elaphe motors
Fundamentally, one of the key advantages of Elaphe’s in-wheel motor technology amounts to this, Gotovac explained: It’s capable of blipping torque delivery—up to its peak torque delivery—almost instantaneously, more precisely than an automaker could with brakes, and in a more extreme way than automakers would ever dare with an inboard motor because of driveshafts and CV joints.
Allowing roll control to be handled by the in-wheel motor system, Gotovac says, would allow automakers to eliminate physical roll bars and their constraints. If you have a motor at each corner, coordinated by a central computer, it’s like having “just one brake in the middle…you feel very safe when you get on ice,” Gotovac explained, or the motors can squeeze at varying levels with just the right timing so as to provide roll control.
Elaphe is currently working toward a very quick 10-kHz modulation cycle and a reaction time of just 4 milliseconds for full torque delivery of its motors. It takes the quickest inboard motor systems 20 times as long to respond, Gotovac claimed, and even then they won’t be able to provide close to full torque. “So that means we really can control with very high bandwidth, a lot of force,” he said, inserting with a smirk: “So we can get very interesting effects.”
Those effects can be quite subtle, he says—like engineering some vibration or tonality back into the driving experience. “We can generate vibration so that you can get a feeling in the car which is engineered but still authentic,” he said, or have the motors generate safety alerts, play songs, or emulate combustion engines—serving a purpose not unlike what Stellantis has engineered for the Dodge Charger Daytona EV.
All of those are things you can’t do with an inboard-motor EV because there are too many other factors with the driveshafts and suspension, and concerns over durability or the harmonics of the gear system.
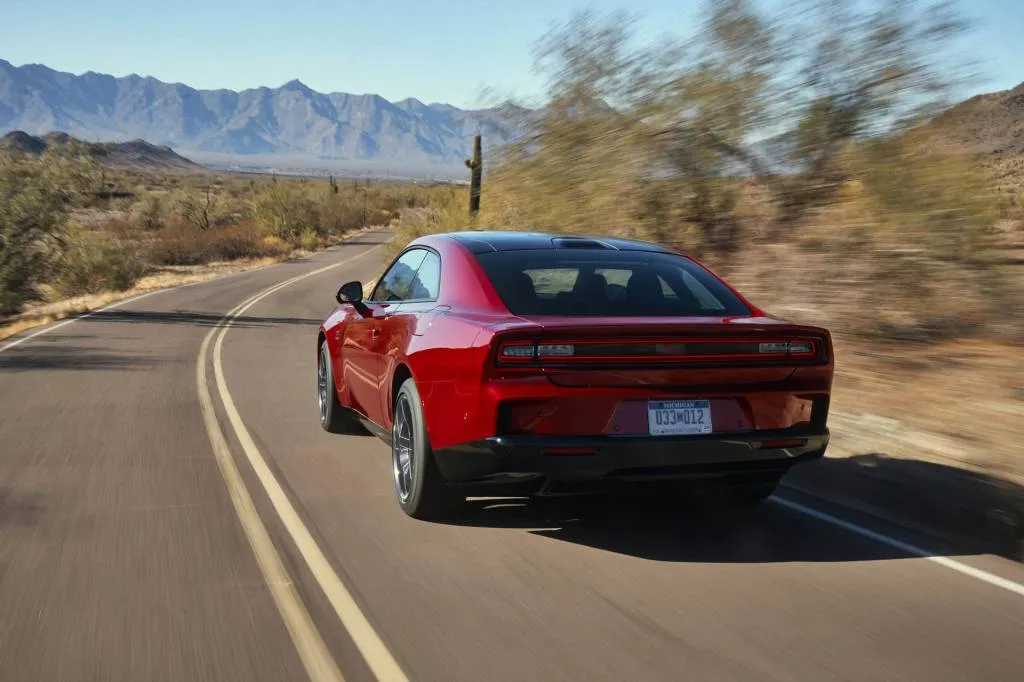
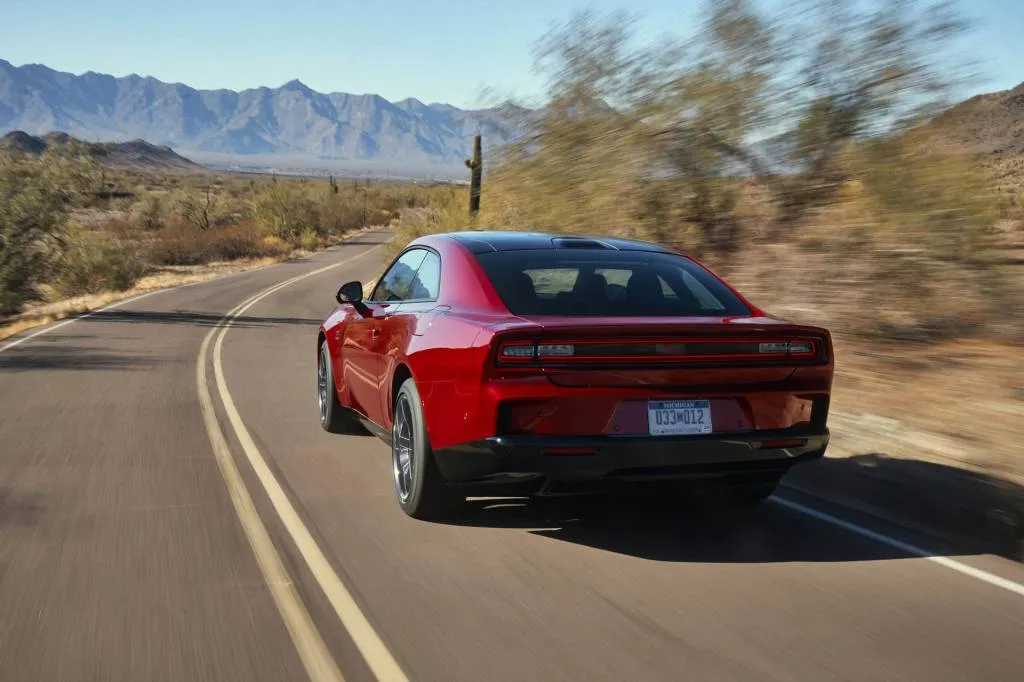
2024 Dodge Charger Daytona
The future: EVs built on platforms for in-wheel motors
None of this tech will be fully realized, Gotovac admits, until we get a new kind of EV, conceived from the start for in-wheel motors. Enabling their potential is a “vehicle-level issue,” he says, and in-wheel motors will only make the vehicle much more efficient if it’s engineered from the ground up for the tech.
If automakers are up for playing this long game with Elaphe, it believes it can lower overall vehicle cost by 20% and boost range and efficiency by 20%—including whole-vehicle design, aerodynamics, chassis controls, and the weight of the car. “That’s where the big potential lies,” Gotovac said.
No major automaker has signed up yet. And what exactly keeps automakers from committing to in-wheel motors on big, mass-market, affordable EV projects sounds like a classic chicken-or-egg dilemma.


Rivian and Volkswagen Group electrical architecture and software stack
Getting to the 20% efficiency boost requires a big investment and commitment that goes beyond the supplier, lamented Gotovac, including an electrical architecture intended to accommodate it. “On the component level we can demonstrate a little bit of efficiency improvement, but not enough for them to make a $5 billion investment,” he added, summing up the predicament.
Gotovac asked rhetorically: “What is the step in between that gets them to believe in this system, so that they engineer that new platform? That’s the thing…”
It’s what drew my attention back to the Sonic 1 motor unit on the pedestal, ready in the meantime to create an Italian exotic that, perhaps, the tech-savvy will recognize for all its firsts.
Source link
Discover more from Autojunction
Subscribe to get the latest posts sent to your email.